


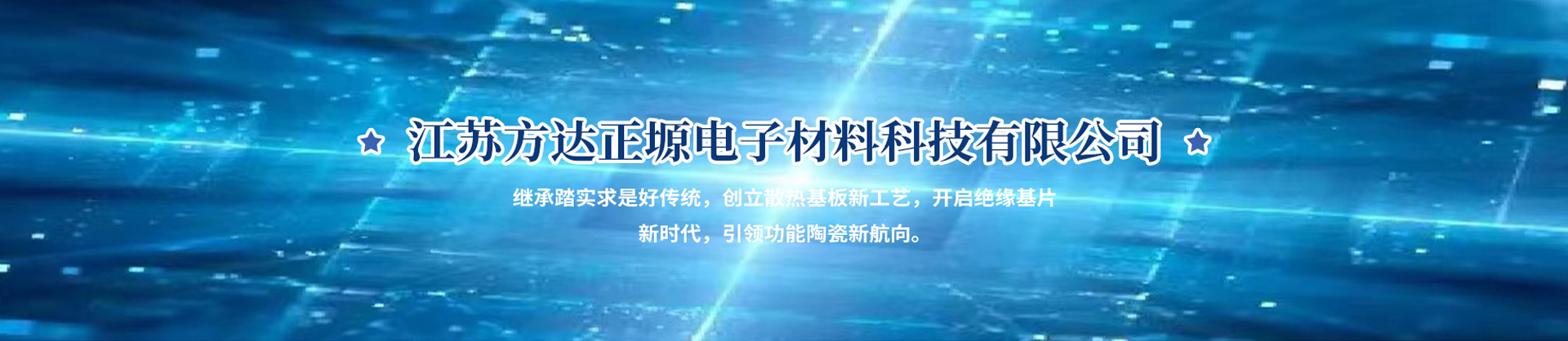
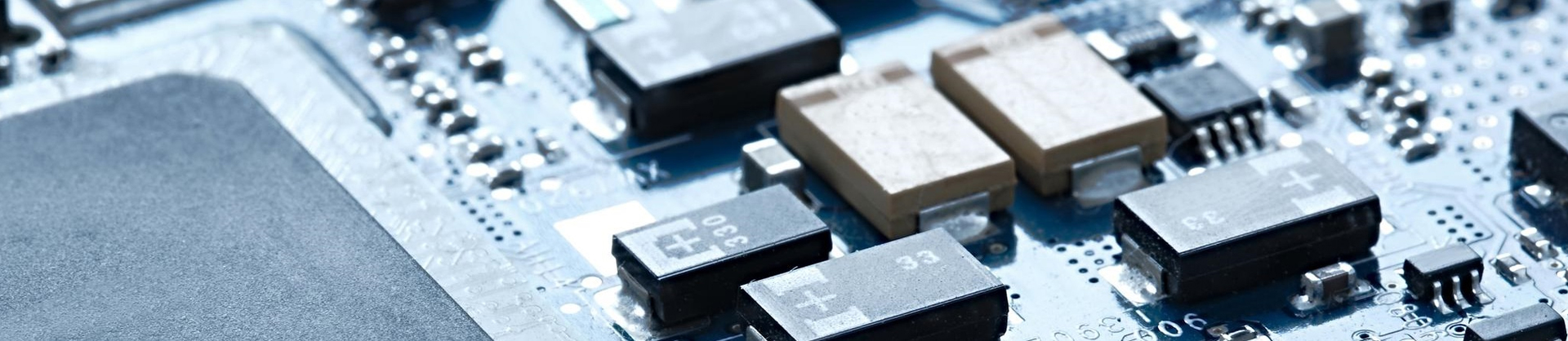
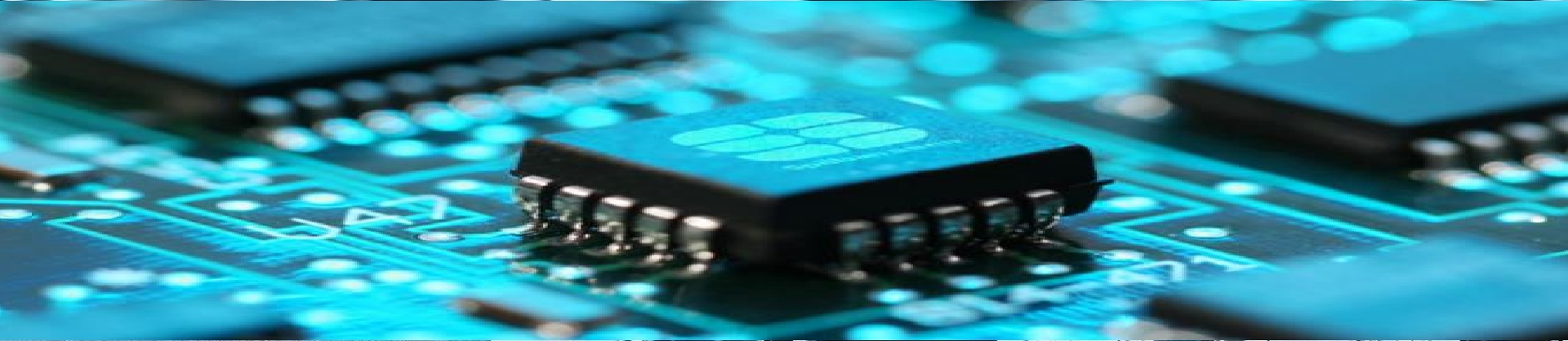
氮化硅微納米粉體的制備
編輯:2022-07-12 15:09:02
一、氮化硅簡(jiǎn)介
氮化硅是綜合性能優(yōu)異的結(jié)構(gòu)陶瓷材料,其硬度大,耐磨性好,耐熱和抗腐蝕性能良好,且具有優(yōu)異的抗熱震性、抗氧化性以及化學(xué)穩(wěn)定性,高溫蠕變小,熱膨脹系數(shù)小,被廣泛應(yīng)用在冶金、航空航天、電子信息、化工機(jī)械以及半導(dǎo)體等行業(yè)。自然界中含有大量的氮元素和硅元素,原料價(jià)格低廉,容易獲取。因此,氮化硅材料的相關(guān)研究對(duì)我國(guó)的現(xiàn)代化建設(shè)具有重要的作用。
制備氮化硅材料的一種重要方法是先合成氮化硅微粉原料,再將其經(jīng)過(guò)成型、熱處理、加工,最終成為制品。因此,氮化硅微粉作為原料,它的特性直接影響著陶瓷材料的一系列性能和應(yīng)用。依據(jù)材料性能的要求,有目的的進(jìn)行氮化硅微粉的制備和粉體性能的控制是當(dāng)前研究的一個(gè)熱點(diǎn)。
二、氮化硅微粉
微粉就是大量固體粒子的集合體。氮化硅粉體 具有多種至關(guān)重要的特性,包括主要成分和微量成分以及各自的濃度、雜質(zhì)的種類及其組成等化學(xué)特性; 還包括顆粒形狀、尺寸及其分布、比表面積、堆積密度、團(tuán)聚狀況、微粉的相態(tài)及其組成等物理特性。下面主要從微粉的化學(xué)成分和粒度兩方面進(jìn)行介紹。
1.化學(xué)組成
氮化硅微粉的化學(xué)成分直接影響著粉體的各種 性能。其中,各成分含量及其均勻性要符合材料的要求,如果某一成分過(guò)量可能會(huì)導(dǎo)致二次重結(jié)晶,甚至阻礙燒結(jié)過(guò)程; 同時(shí),適量的添加一些成分可以促進(jìn)粉體的制備。有研究人員在硅粉直接氮化法制備氮化硅微粉的過(guò)程中,選用 Fe、Al、Ca 作為添加劑,促進(jìn)了硅粉的氮化,并成功合成了純度高于99%的 α-Si3N4微粉。有研究人員以 CaF2為添加劑,添加量<4% ,直接氮化得到了準(zhǔn)球形 β-Si3N4 微粉。另外,微粉的純度也對(duì)其性能有不可忽視的影響,雜質(zhì)的種類和比例越少,粉體的性質(zhì)就越優(yōu)異,特別要防止雜質(zhì)的局部聚集。
2.粉體的粒度
氮化硅微粉的粒度以及顆粒尺寸分布直接影響其燒結(jié)過(guò)程和材料性能。研究表明,在一定的燒結(jié)溫度下,燒結(jié)速度與粉體顆粒半徑的 n 次方成反比。因此,粒度越小,燒結(jié)速度越快。但粒度過(guò)小會(huì)導(dǎo)致嚴(yán)重團(tuán)聚,同時(shí)粉體的堆積密度大大降低,并且吸附 帶入空氣中的雜質(zhì)顆粒,反而不利于燒結(jié)。此外,顆粒的尺寸分布影響著燒結(jié)之后的致密度。顆粒尺寸差別大,會(huì)導(dǎo)致燒結(jié)后的部分區(qū)域不致密,較大顆粒還會(huì)導(dǎo)致二次重結(jié)晶,嚴(yán)重影響氮化硅陶瓷的性能。因此,應(yīng)該控制粉體的顯微結(jié)構(gòu),盡量使粉體的顆粒尺寸分布窄且大小均勻。
3.制備方法
氮化硅微粉的制備方法主要包括固相反應(yīng)法、液相反應(yīng)法和氣相反應(yīng)法。這三類方法各有利
弊,需要根據(jù)實(shí)際生產(chǎn)需求選擇和完善。
(1)固相反應(yīng)法
固相反應(yīng)法采用比較早,技術(shù)相對(duì)成熟,成本比較低,應(yīng)用也更加廣泛。主要包括硅粉直接氮化法、碳熱還原氮化法和自蔓延法。
(2)硅粉直接氮化法
硅粉直接氮化法是最早用來(lái)制備氮化硅粉末的一種方法,適合大規(guī)模工業(yè)生產(chǎn),但是所得粉體粒度大,必須經(jīng)過(guò)機(jī)械研磨粉碎后才可獲得微粉。具體方法是將高純硅粉置于反應(yīng)爐中,通入氮?dú)饣虬睔?,或是二者混合氣體,在1 200~1 400 ℃下發(fā)生氮化反應(yīng),以此合成氮化硅粉末。
(3)碳熱還原氮化法
碳熱還原氮化法以二氧化硅和碳作為原料,在 1 427 ℃的氮化溫度下,通入氮?dú)饣虬睔膺M(jìn)行反應(yīng),得到的氮化硅粉末純度高、粒度小、α -Si3 N4 含量高,且反應(yīng)速率快,比較適合工業(yè)化批量生產(chǎn),但可能含有 SiC、Si2 N2 O 和 SiN 等雜質(zhì),且粒度不均勻,這極大的影響了后續(xù)燒結(jié)制備氮化硅陶瓷的性能。
(4)自蔓延法
自蔓延法最早由前蘇聯(lián)學(xué)者在 60 年代提出,于70 年代發(fā)展至今。具體方法是將原料粉末成型后,在一端點(diǎn)燃,引發(fā)高熱反應(yīng),自行推進(jìn)至完全反應(yīng)。該方法在 0. 6 ~ 0.7 MPa 的低氮?dú)鈮合逻M(jìn)行,不需要外部提供能源,可以得到顆粒尺寸在 1~2 μm的高純氮化硅微粉,反應(yīng)中要加入適量的 Si3N4作為晶種。該方法的優(yōu)點(diǎn)是反應(yīng)速度快,硅粉可在100~200 s 內(nèi)完全氮化,且節(jié)能環(huán)保,雜質(zhì)少,純度高。
(5)液相反應(yīng)法
液相反應(yīng)法是工業(yè)和實(shí)驗(yàn)上應(yīng)用最為廣泛的合成氮化硅微粉的方法之一。其反應(yīng)速率較快,粉體粒度比較均勻,顆粒較細(xì),近年來(lái)發(fā)展迅速,但純度不易控制,且成本比固相反應(yīng)法的高,仍需不斷的改善。主要包括熱分解法和溶膠-凝膠法。
(6)熱分解法
熱分解法是以氯化硅先在 0 ℃的干燥乙烷中與無(wú)水氨氣反應(yīng)生成固態(tài)氨基硅,再在1 400 ~ 1600 ℃下熱分解,從而獲得高純 α -Si3N4微粉。反應(yīng)方程式如下:
SiCl4 ( l) + 6NH3 ( l) === Si( NH) 2 ( s) + 4NH4Cl( s)
3Si( NH) 2 ( s) === Si3N4 ( s) + 2NH3 ( g)
3Si( NH) 4 ( s)=== Si3N4 ( s) + 8NH3 ( g)
(7)溶膠-凝膠法
溶膠-凝膠法制備氮化硅微粉,是使原料在溶膠狀態(tài)充分混合,從而獲得高純氮化硅微粉的方法。相對(duì)于碳熱還原氮化法,其解決了二氧化硅顆粒粗以及與炭黑難以混合均勻的問(wèn)題,并且常與碳熱還原氮化法聯(lián)合使用。
(8)氣相反應(yīng)法
氣相反 應(yīng) 法 是 以 SiH4 之類的硅氫化物或者 SiCl4之類的鹵化物作為硅源,以 NH3作為氮源,在高溫氣態(tài)下合成氮化硅微粉的方法。其可以根據(jù)激發(fā)方法的不同分為高溫化學(xué)氣相沉積法、激光誘導(dǎo)化學(xué)氣相沉積法、等離子體增強(qiáng)化學(xué)氣相沉積法。
(9)高溫化學(xué)氣相沉積法
高溫化學(xué)氣相沉積法是以 SiH4或 SiCl4和 NH3 為原料,在 1 100 ~ 1 500 ℃ 的高溫下加熱激發(fā)反應(yīng)進(jìn)行,可以獲得高純、超細(xì)的 α -Si3N4微粉,且操作簡(jiǎn)單,但是產(chǎn)率較低,溫度越高,粒徑比越大,越難以獲得粒徑小于 20 nm 的氮化硅超微粉。在用高溫化學(xué)氣相沉積法制備 Si3N4薄膜及涂層的相關(guān)研究中 發(fā)現(xiàn),通過(guò)控制溫度可以加快沉積速率,并提高致密度,最適合的溫度在 750 ~ 950 ℃之間
(10)激光誘導(dǎo)化學(xué)氣相沉積法
激光誘導(dǎo)化學(xué)氣相沉積法是以 CO2激光器激發(fā)反應(yīng)進(jìn)行,可以合成粒徑小于 50 nm、粒度分布窄、高純的無(wú)定形氮化硅微粉,優(yōu)點(diǎn)是避免污染,容易高度控制反應(yīng),但是成本較高,且在溫度較低時(shí)SiH4會(huì)發(fā)生解離,導(dǎo)致氮化硅微粉游離硅含量過(guò)高。研究人員通過(guò)雙光束激發(fā),提高激光功率密度,采用 NH3 /SiH4 >8 的方法,解決了這一問(wèn)題,獲得了高純氮化硅微粉。
4.技術(shù)攻關(guān)方向
近年來(lái),氮化硅材料由于具有高熱導(dǎo)率、熱膨脹系數(shù)小等特點(diǎn)被認(rèn)為是最具有潛力的電子散熱材料,但是氮化硅粉體原料不能滿足制備高性能氮化硅材料的需求,而具有納米級(jí)的氮化硅超微粉可以增加燒結(jié)后的強(qiáng)度和韌度,提高彈性模量。因此,合成納米級(jí)氮化硅的方法及其相關(guān)研究具有重大意義。
納米級(jí)氮化硅材料的合成普遍成本較高,難以批量化生產(chǎn)。研究人員通過(guò)給硅粉進(jìn)行造粒預(yù)
處理,再直接氮化的方法,顯著增大了 Si3N4納米線生長(zhǎng)空間,得到了直徑為 80 ~ 150 nm,長(zhǎng)徑比為 20 ~ 50,含量為 95% Si3N4的納米線,并且顯著提高了氮化速率,為納米級(jí)氮化硅材料的低成本、工業(yè)化生產(chǎn)做出了一定的貢獻(xiàn)。
近年來(lái),隨著中國(guó)制造和高端機(jī)械化的不斷發(fā)展,對(duì)氮化硅材料的需求日益增加,如何低成本、批量化制備出理想粒度、純度以及兼具諸多優(yōu)良特性的氮化硅微粉和納米級(jí)超微粉成為無(wú)機(jī)非金屬材料領(lǐng)域的研究熱點(diǎn)。就氮化硅微粉制備而言,未來(lái)發(fā)展方向可從以下 4 個(gè)方面著手:
(1)原料
應(yīng)尋找更優(yōu)良的原料,或者改善原料的物理化學(xué)特性; 選擇更綠色、環(huán)保、低成本的硅源和氮源,控制原料的粒度和均勻性。
(2)添加劑
應(yīng)選用合適的稀釋劑、添加劑輔助氮化反應(yīng)進(jìn)行,提高氮化硅微粉的性能。
(3)純度
應(yīng)嚴(yán)格控制雜質(zhì)含量,提高氮化硅微粉的純度; 同時(shí),應(yīng)挖掘適量且利于燒結(jié)的有益雜質(zhì)。
(4)反應(yīng)條件
應(yīng)改善氮化反應(yīng)進(jìn)行的條件,如: 氮化溫度、氮?dú)鈮毫傲髁俊⒎磻?yīng)氛圍以及反應(yīng)設(shè)備等,以制得理想的氮化硅微粉